

LTCM
Reduce time and cost; increase precision and efficiency.
OUR VISION
Our focus at LTCM is on developing better building systems that increase accuracy, quality and compliance, while saving time, and reducing overall costs. Our internationally patented Load Transfer Construction Method (LTCM) uses a fully documented construction process to deliver efficient, engineered buildings.
At LTCM, we aim to build clever.
What is LTCM? LTCM refers to the Load Transfer Construction Method, our patented complete superstructure building system.
At LTCM Australia, we have developed an innovative building system that employs existing components in a highly efficient building methodology, designed to increase the speed, accuracy, and compliance of the construction process. We have specifically sought to use existing components (such as light-weight steel framing) that are widely used and available within the local construction industry, as these components are already proven within the Australian market. Furthermore, working with existing technology ensures that there is a well-established supply chain for these components within the local construction industry.
ABOUT LTCM


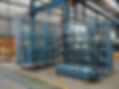





LTCM (Load Transfer Construction Method) is an innovative building methodology that combines the structural integrity of a concrete-framed superstructure with the speed and efficiency of a light-gauge steel framing build.
The LTCM system is underpinned by the concept of the ‘load transfer’ within the superstructure of the building. ‘Load transfer’ refers to the way in which structural loads or forces applied to the superstructure of the building are redirected during the construction process. Our system transfers the structural load of the building from the prefabricated steel framing (supported by engineer specified props and bracing) to the concrete framing (consisting of decks, slabs and columns) that make up the final load bearing superstructure.
The result is a high-quality concrete-framed building with strong non-load-bearing light-weight steel framed internal walls.
TRANSFERRING THE LOAD
Initially, the base of the superstructure is formed from 3D modelled prefabricated light-weight steel framing by the installer. The framing is manufactured off-site and delivered to a ‘just-in-time’ program. As the build progresses, the light-weight steel framing is incorporated into the next phase of the LTCM system – the reinforced concrete superstructure made up of reinforced concrete decks, columns, prefabricated lift shafts and cores.
At this point in the process, the steel framing is taking the structural load (supported by braces and props) and there is not requirement for the concrete to reach structural strength before the installation of the next level of light-weight steel framing. This drastically reduces the floor-to-floor cycle, which can commence the day after the concrete pour for each slab.
Once the concrete has reached structural strength and sign-off has been achieved, the installer can carry out the quick and efficient process that disengages the framing and redirects the structural load from the light-weight steel framing to the reinforced concrete superstructure.
SECONDARY FUNCTION - INCREASED EFFICIENCY
The disengaged light-weight steel framing then takes on its secondary function as non-load-bearing internal and external wall framing. These wall frames can be finished and lined to the developer or architect’s specification. Similarly, the non-load-bearing steel framing on the exterior of the building can be fitted with any conventional façade treatment, including our own thin-shell concrete façade pre-cast panels.
By simultaneously streamlining the building process and maximising the efficiency of the embedded concrete columns and the steel framing, the LTCM system can deliver multiple floors within a short time frame to finishing trades, saving time, and increasing productivity on site. The precision concrete framing enables concurrent manufacturing of off-site elements, like windows and cabinetry, allowing builders to condense the overall time-frame of the build.
VERTICAL INTEGRATION
At LTCM we have worked to vertically integrate our system by developing a series of interconnected products that can deliver walls, ceilings, decks and slabs, pre-cast columns, lift shafts, cores, ceiling linings, pre-cast thin shell façade panels, bathroom pods and roof structures. Our products have been carefully designed to work with smaller, mobile cranes were possible, enabling easier access to tight or difficult sites.
Our locally manufactured prefabricated bathroom pods are an especially exciting product range that enables the off-site production of high-end bathrooms, finished to the specification of the developer or architect. Ideal for apartments and hotels, the bathroom pods can be seamlessly integrated into the light-weight steel framing and screeded to a level threshold transition with the same finished floor level as the rest of the apartment or hotel room.
PROVEN COMPONENTS
In developing LTCM, we have carefully considered the role that each individual component and process plays within the construction of a concrete-frame building and worked to maximise their efficiency. As a result, our system is designed using existing software such as Revit, and manufactured using widely used, readily available components, which are used in our streamlined LTCM methodology to deliver significant time savings.
We have deliberately sought to employ existing construction technology and components, to reduce the overall cost of the system and to ensure that your builder can continue to use their own, well-established supply chains for the components in the local construction industry. Using time-proven components, products and technologies also ensures that developers, architects, builders, and clients can be assured of the quality, safety, and longevity of the finished project.
DOCUMENTATION & COMPLIANCE
At LTCM, we have recognised the increasing importance placed on the documentation of the building process. To address this critical issue, the LTCM system assembly procedure involves a documentation process that commits the builder to following the correct procedure, includes ITPs, and forms a warranty documentation on completion.

OUR PRODUCTS & SERVICES
A vertically integrated system from deck to roof.
WALL FRAMING
DECKING
ROOFING
BATHROOM PODS
LIFT SHAFTS & CORES





ADVANTAGES OF LTCM
Reduce time and cost; increase precision and efficiency.
Utilises existing components with well-established supply chains in local construction industries
LTCM systems open multiple floors or workfaces to finishing trades, affording earlier practical completions
Precision design and off-site manufacturing drastically reduces wastage, saves on material costs, and reduces the space required to hold materials on site
Documented LTCM process reduces the risk of non-compliant projects on completion
Precision concrete framing enables concurrent manufacture of offsite elements such as windows and cabinetry, reducing overall build time
Architects can design in the 3D modelling software of their choice. LTCM can manufacture direct from 3D modelling software
LTCM will use the 3D model to specify the components required for the build
A LTCM approved facility will produce the frames and components, ready for installation on-site
BUILDING WITH LTCM
Our specialised team can work with you to get the job done.
Download our LTCM Revit families
Design direct from the 3D modelling software of your choice
LTCM system superstructure installed on-site
